RECLADDING THE SPENCER ON BYRON REQUIRED A RAPID RESPONSE TO CHANGES AS EXISTING CLADDING WAS REMOVED, AND EFFECTIVE TEAM COLLABORATION TO MEET A RIGOROUS TIME FRAME.
The external cladding system on The Spencer on Byron Hotel, a 21-storey hotel and apartment building in Takapuna, no longer met the requirements of the New Zealand Building Code. Symonite was brought on board by Brosnan Construction to deliver on an extensive remediation programme of the façade, while ensuring the hotel was fully operational to avoid significant revenue loss to the owner.
The value of input at the pre-design stage
‘Symonite was our preferred contractor on the project as the scope of work matched their expertise and the type of façades they specialise in,’ says Gary Board, site manager for Brosnan Construction. Symonite was engaged during the pre-design stage and created a full mock-up of the façade design before the system was signed off.
‘We worked on the detailing and engineering throughout the process, including balcony details, so we could achieve consent with a full set of shop drawings,’ says Andrew Philpott, project manager at Symonite.
An innovative waterproof rainscreen in composite aluminium
The façade is a waterproof rain screen over a James Hardie weathering line. The aluminium cladding used was 3 mm-thick Reynodual – a coil-coated, double-sheet aluminium panel for facades that has high technical, visual and environmentally friendly attributes. Innovations lie in the detailing of the facade design. ‘Outside, you just see a flat panel, but it’s the infrastructure and how it’s built up in behind that counts,’ says Board.
The challenge of adapting to a changing design
During construction, one of the biggest challenges the team faced were the design adjustments required, as the true structure and geometry of the building was revealed. ‘Symonite adapted easily and had the technical expertise in-house to tailor solutions to any unforeseen situations and design changes,’ explains Board.
On large-scale projects, there is a lot of repetition, so even one small change can have a compounding effect. ‘Each time this happened, Symonite would come up with a solution, go through consenting, before proceeding with the work,’ he says.
The process of constructing the façade – floor by floor
The installation of the façade mostly utilised standard details. One difference though was a secondary fixing support designed to avoid fixing the aluminium panels directly to the structure, thus giving a secondary moisture-control line.
‘A custom-built external scaffold was winched up the building as we progressed, so our team could gain access to two floors at a time for optimal construction speed and sequencing,’ explains Philpott. ‘We started at the podium level, then our team worked its way up floor by floor. The fabrication team worked two days ahead of us, so we had panels ready to install when we needed it.’
Transparency, approachability and integrity on the job
Given the scale of the project, the physical logistics on site required close collaboration between all team members, with the programme methodology tailored with Symonite’s input.
‘The teams had to work across multiple stages, which ran concurrently, so we had to be very organised with a high degree of collaboration,’ says Board. ‘We had a harmonic relationship with Symonite. We held weekly coordination meetings and they were always present. They took the project seriously and were committed to it – a work ethic that stems from integrity. They are a very approachable company – from site level to senior management.’
—
CREDITS
Project: Spencer on Byron Hotel
Architect: Babbage, Ignite Architects
Main Contractor: Brosnan Construction
Façade Engineer: Lautrec
Product & Services: Full design and installation of Aluminium Composite Panel. Reclad.
Photographer: Mark Scowen
Writer: Folio
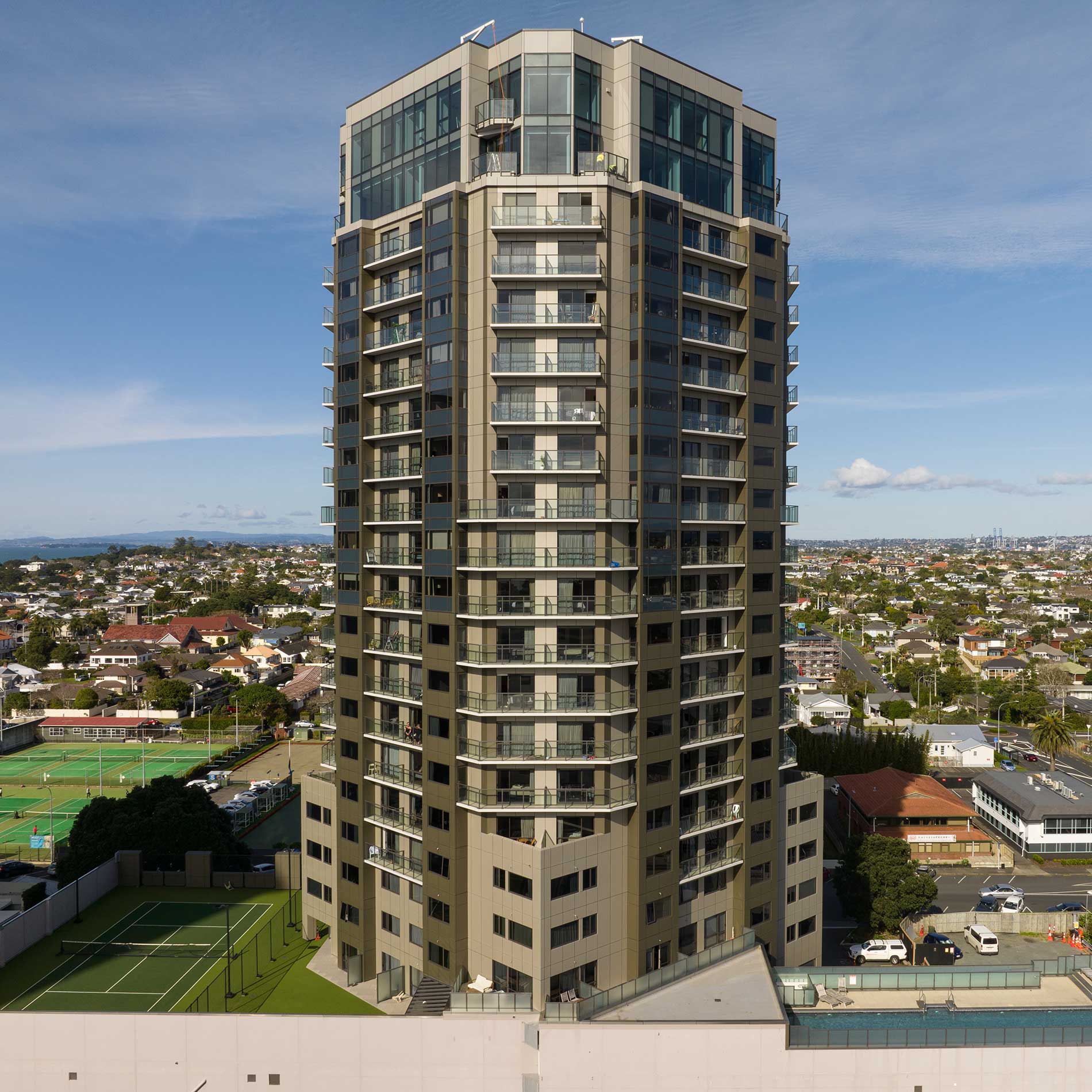
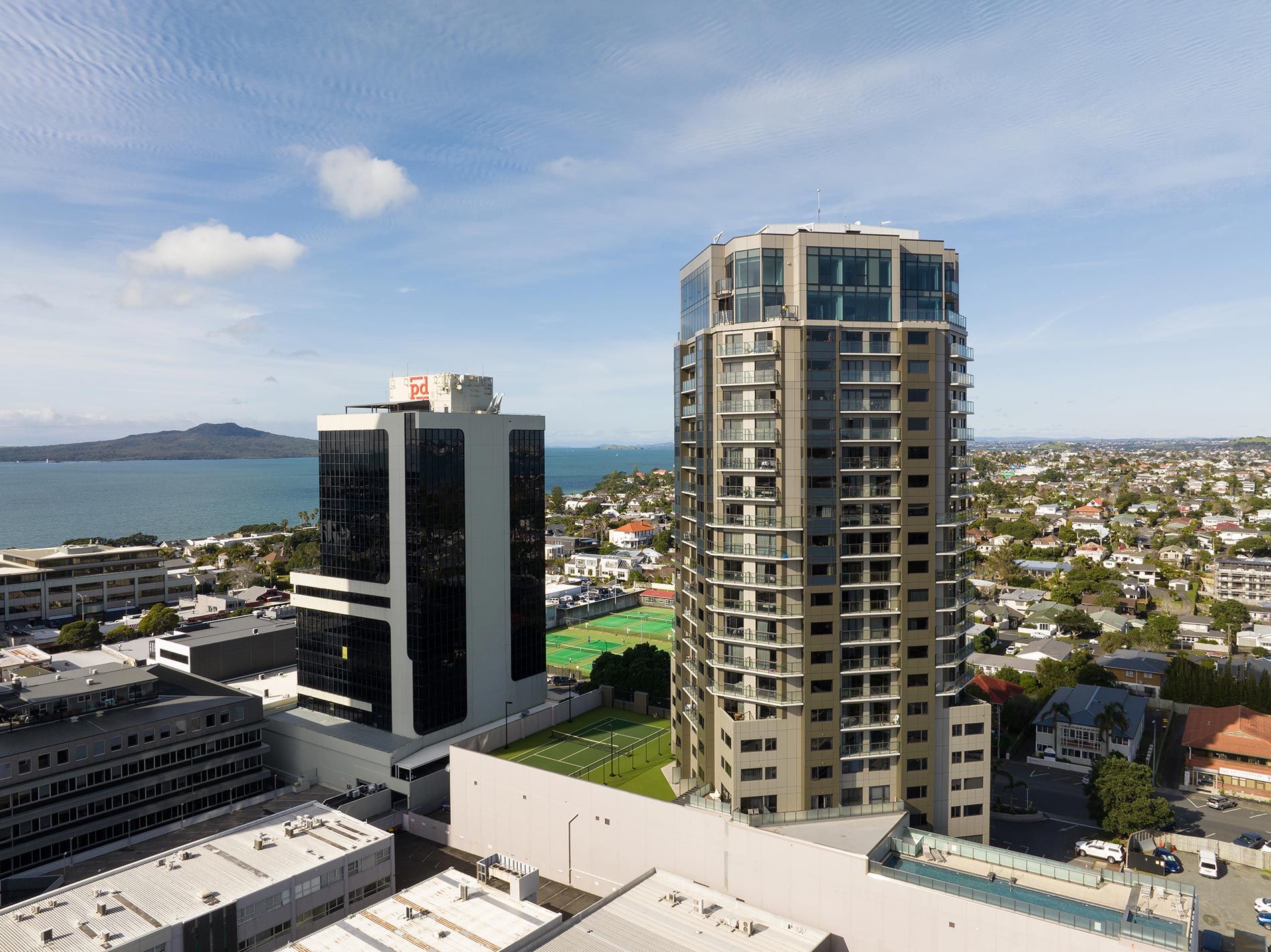
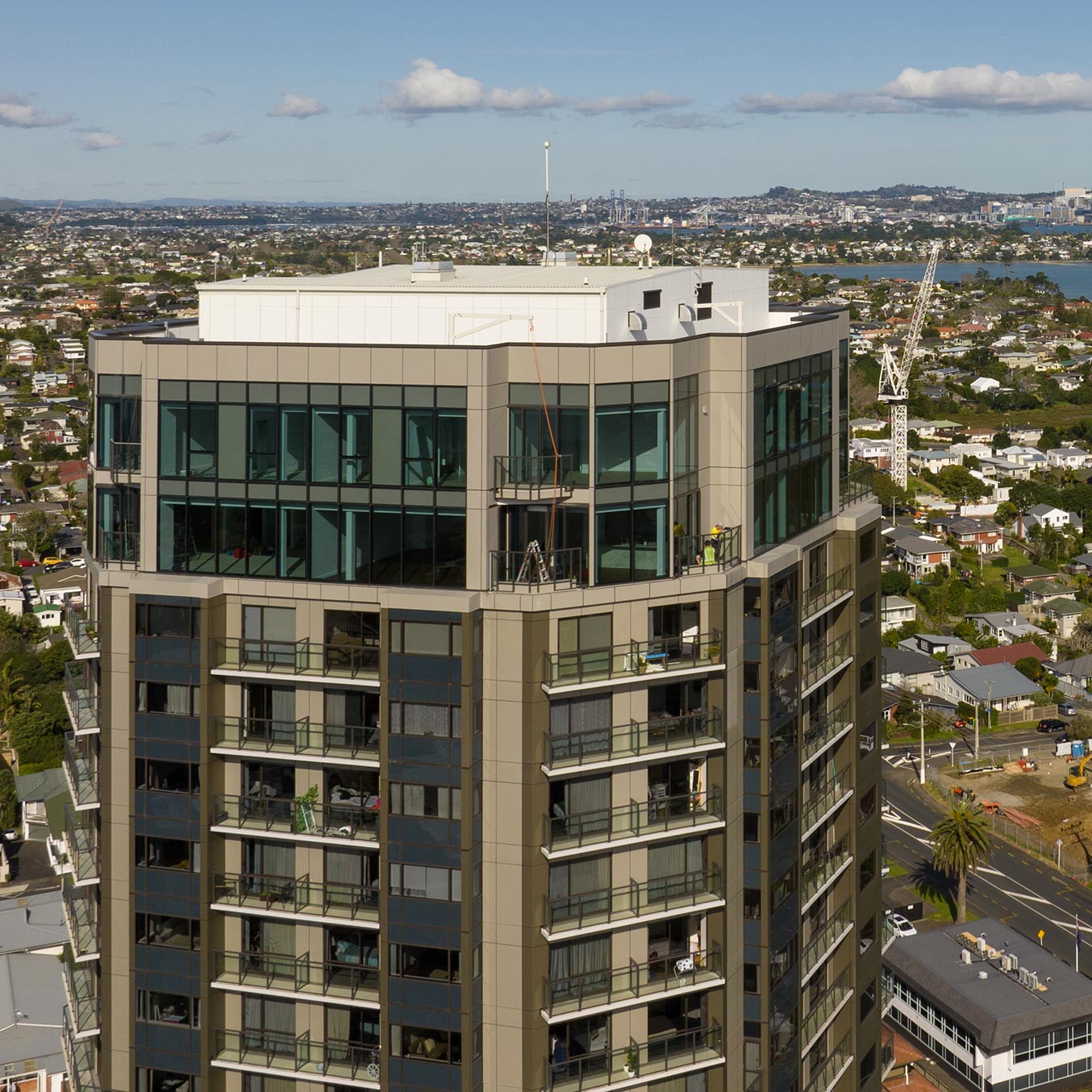